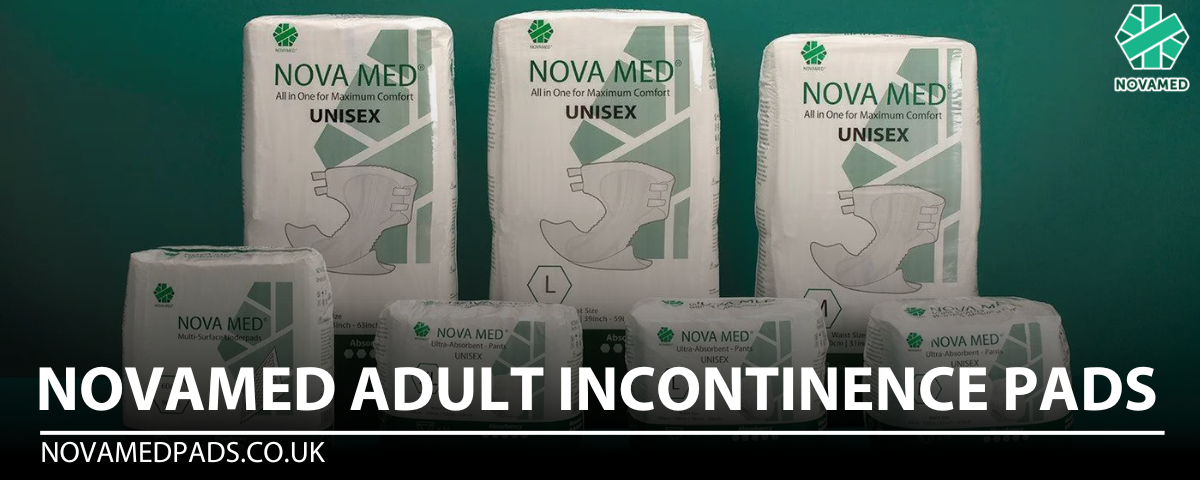
Novamed Adult Incontinence Pads
At Novamed, we are committed to providing high-quality adult incontinence pads that offer excellent leakage protection and support skin health.
We believe that innovation and comfort are key to improving healthcare. With the aim to enhance the quality and accessibility of medical products, we proudly introduce our range of Novamed Adult Incontinence Pads.
Advanced Technology for Maximum Absorbency
Our adult incontinence products are designed and manufactured using the latest technological advancements. Each pad features a top sheet, acquisition layer, SAP, fluff, and a laminated bottom sheet with breathable sides, ensuring maximum comfort and protection.
How Our Incontinence Pads Work
The acquisition layer, located under the top sheet, is the first layer that comes into contact with urine. It quickly absorbs and distributes the urine to the storage core (comprised of SAP and fluff), preventing surface leakage. This layer handles multiple gushes without compromising its absorbency, ensuring optimal protection.
The dual core system consists of both a top and bottom core. The top core contains a higher concentration of super absorbent polymers (SAP), which delivers enhanced absorbency where it's needed most. Meanwhile, the bottom core, with more fluff, locks away wetness throughout the pad.
The Process Behind Manufacturing Adult Nappies
Disposable adult nappies feature an absorbent pad sandwiched between two layers of nonwoven fabric. The absorbent core is engineered to retain body fluids, while the nonwoven fabric shapes the nappy and prevents leakage. The multi-step manufacturing process includes forming the absorbent pad through vacuum forming, attaching it to the permeable top sheet and impermeable bottom sheet, and sealing the components with heat or ultrasonic vibrations.
Key Materials in Novamed Adult Nappies
-
Absorbent Pad: The pad, a key component, absorbs and retains moisture efficiently. Modern disposable nappies absorb up to 15 times their weight in water due to super absorbent polymers. These polymers form a gel network that locks in fluids, preventing leakage.
-
Non-Woven Fabric: Our nappies use nonwoven fabrics made from plastic resins like polypropylene and polyethylene, assembled using processes such as the meltdown method. This ensures the nappy is both permeable on top and impermeable on the bottom, offering both comfort and protection.
-
Additional Components: Elastic fibres, adhesives, and closure strips like Velcro or tape are also integrated into the design, ensuring a snug, leak-proof fit.
The Manufacturing Process in Detail
-
Formation of the Absorbent Pad: Pressurised nozzles spray fibres and absorbent polymers onto a perforated conveyor, where the vacuum helps form a flat pad. The fibres and polymers are layered to create a core that effectively prevents gel blocking and retains moisture.
-
Nonwoven Fabric Formation: Using the meltdown process, we produce three sheets of nonwoven fabric: a top sheet, bottom sheet, and a backing sheet. These sheets are cut, assembled, and integrated with the absorbent core, elastic bands, and adhesive to form the finished nappy.
Once the assembly is complete, the nappies are cut, folded, and packaged for distribution.
By incorporating super absorbent polymers, advanced dual core technology, and a precise manufacturing process, Novamed Adult Incontinence Pads deliver superior leakage protection, maximum comfort, and long-lasting reliability.
Written by: Mrs Julie Collett
Retired Continence Nurse Specialist
Bladder and bowel incontinence may be caused by conditions which can be treated medically. Please consult your physician for medical advice and guidance.